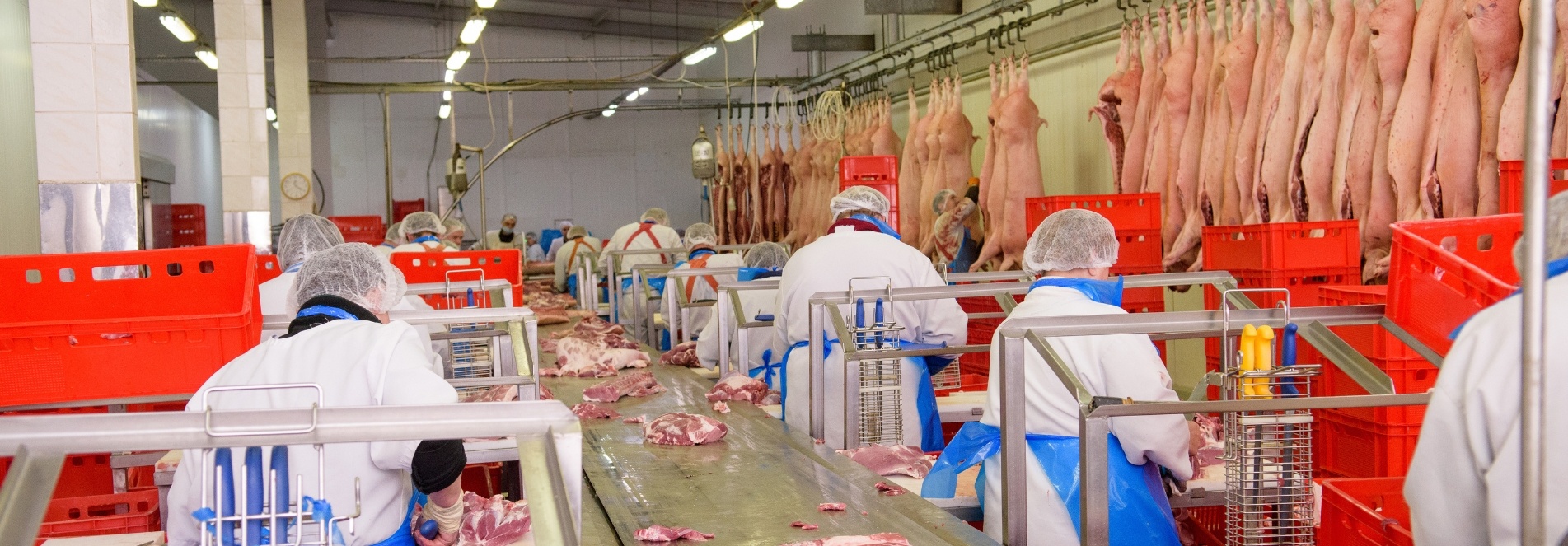
Combining AI and a Connected Workforce for Workplace Safety and Optimization
Enhancing Workforce Management and Safety with RFID Technology at JBS Foods
Customer Case: JBS
Managing a large workforce in the food processing industry, especially under the stringent requirements of Brazil's NR36 regulations, presents significant challenges. NR36 is designed to protect the health and safety of workers in meat processing plants, with strict guidelines on exposure times, rest breaks, thermal comfort, PPE, and medical monitoring. To address these challenges, JBS Foods has implemented an innovative solution using RFID technology integrated with SmartXHUB, revolutionizing workforce management for over 2,000 employees working in three shifts.
JBS Foods, headquartered in Brazil, is one of the largest food processing companies globally, specializing in beef, pork, chicken, and lamb products. The company operates in over 20 countries, managing more than 400 production units and employing around 250,000 people. JBS processes over 200,000 cattle, 400,000 hogs, and 13 million birds daily. Its extensive portfolio includes brands like Swift, Pilgrim’s, Seara, and Moy Park, catering to a diverse range of markets worldwide. JBS's commitment to sustainability, innovation, and food safety has positioned it as a key player in the global food industry, with annual revenues exceeding $50 billion.
The Challenge
JBS Foods operates in a highly regulated environment where ensuring worker safety and compliance with NR36 regulations is critical. Managing the schedules, productivity, and safety of thousands of workers across multiple shifts requires precise and efficient systems. Additionally, monitoring individual and collective risks, managing entry and exit times, and ensuring workers take required breaks are essential to maintaining a safe and productive work environment. Furthermore, legal issues arise when workers file claims against the company for occupational diseases. These cases often stem from alleged non-compliance with safety regulations, leading to substantial legal and financial liabilities for the company. Ensuring rigorous adherence to NR36 standards is crucial to mitigating these risks.
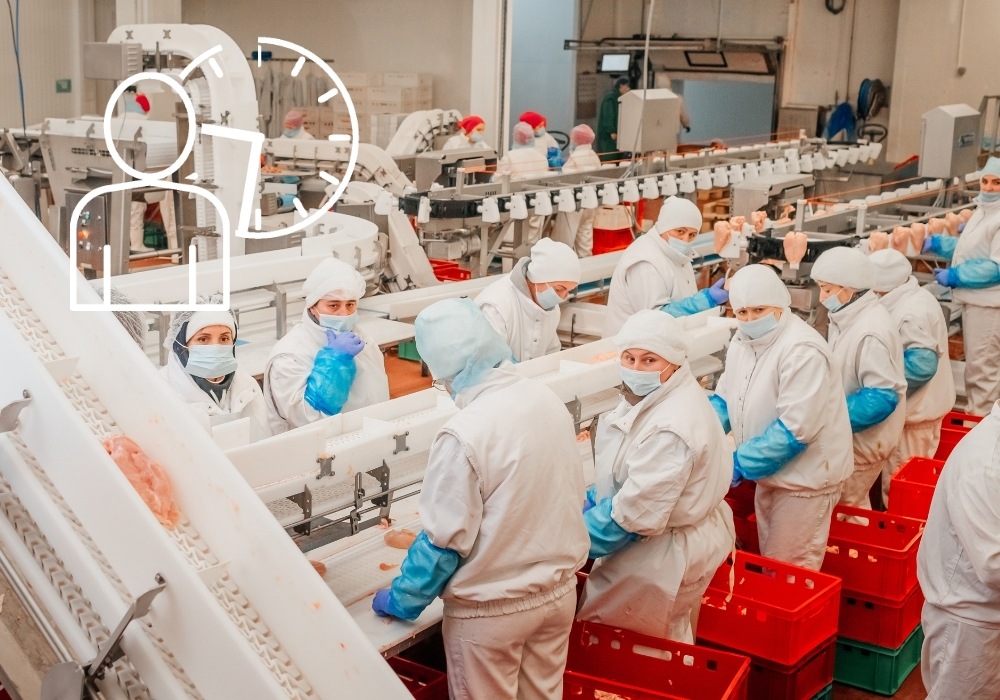
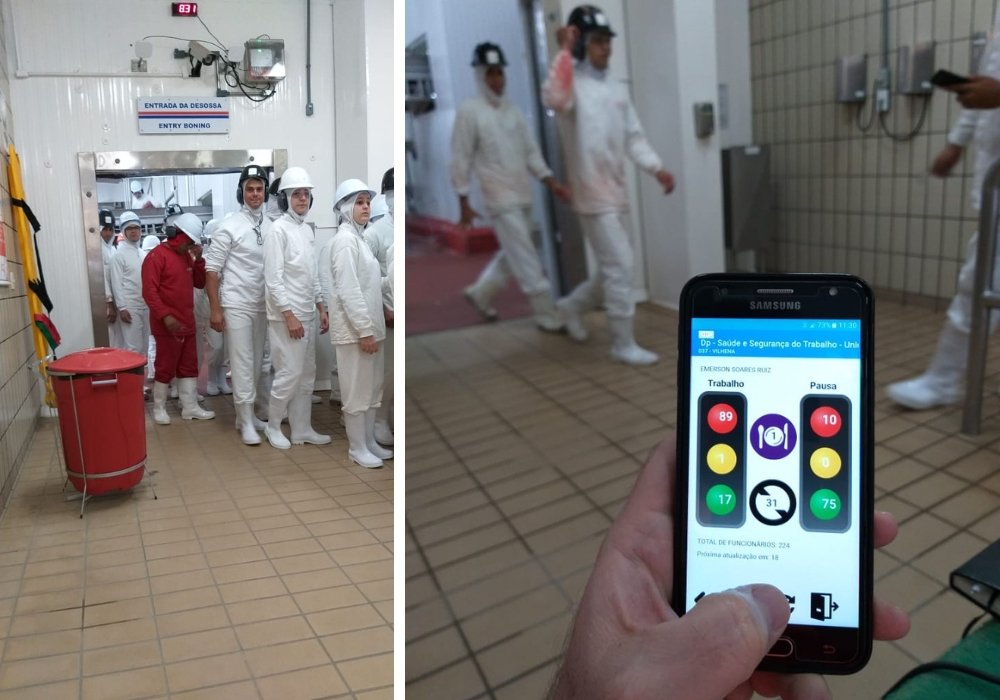
The Solution
To meet these demands, JBS Foods deployed SmartXHUB, an advanced workforce management system that uses RFID technology. This system integrates seamlessly with the company’s HR solutions, providing a comprehensive approach to managing worker schedules, productivity, and safety.
Key aspects of the solution include:
- RFID-Enabled PPE: Each worker is equipped with PPE embedded with RFID tags, allowing for real-time tracking of their movements and activities.
- Strategic RFID Readers: Over 15 RFID readers are placed in key locations throughout the facility, ensuring accurate monitoring of entry and exit times and tracking worker movements within the plant.
- Integrated Management Dashboard: A centralized dashboard accessible via a smartphone app provides managers with real-time data and insights into worker attendance, productivity, and compliance with safety regulations.
- Legal Compliance and Documentation: The system ensures thorough documentation of safety practices and compliance with NR36, reducing the company’s vulnerability to legal claims related to occupational diseases. This documentation is critical in defending against worker lawsuits, demonstrating that the company adheres to all required safety standards.
Key Benefits of SmartXHUB for JBS Foods
- Real-Time Monitoring and Compliance: RFID technology enables precise tracking of worker movements, ensuring compliance with NR36 regulations by monitoring exposure times, break periods, and PPE usage.
- Enhanced Safety and Risk Management: The system tracks individual and collective risks, helping to prevent accidents and health issues by ensuring workers adhere to safety protocols and take mandated breaks.
- Seamless HR Integration: SmartXHUB integrates with the HR system to manage worker schedules, certifications, and training, ensuring all personnel are qualified and compliant with safety standards.
- Operational Efficiency: Real-time data and insights allow managers to optimize workforce deployment, monitor productivity, and respond quickly to issues, enhancing overall operational efficiency.
- Legal Protection: By ensuring rigorous compliance with NR36 and maintaining detailed records, the system helps mitigate legal risks associated with occupational health claims, protecting the company from potential lawsuits.
Implementation and Results
The implementation of SmartXHUB at JBS Foods involved rigorous testing and validation to ensure the system’s reliability and effectiveness in real-world conditions. The deployment included equipping workers with RFID-enabled PPE, installing RFID readers, and integrating the system with the existing HR platform.
The results have been impressive:
- Improved Compliance and Safety: The system ensures adherence to NR36 regulations, significantly reducing safety incidents and ensuring all workers have up-to-date certifications and training.
- Enhanced Monitoring: Real-time tracking and automated alerts provide a comprehensive view of worker movements and safety status, enabling quick responses to potential hazards.
- Increased Operational Efficiency: The system reduces paperwork and administrative burdens, allowing staff to focus on critical tasks and improving overall productivity.
- Legal Risk Mitigation: Thorough documentation and real-time compliance monitoring significantly reduce the company’s exposure to legal claims related to worker health and safety.

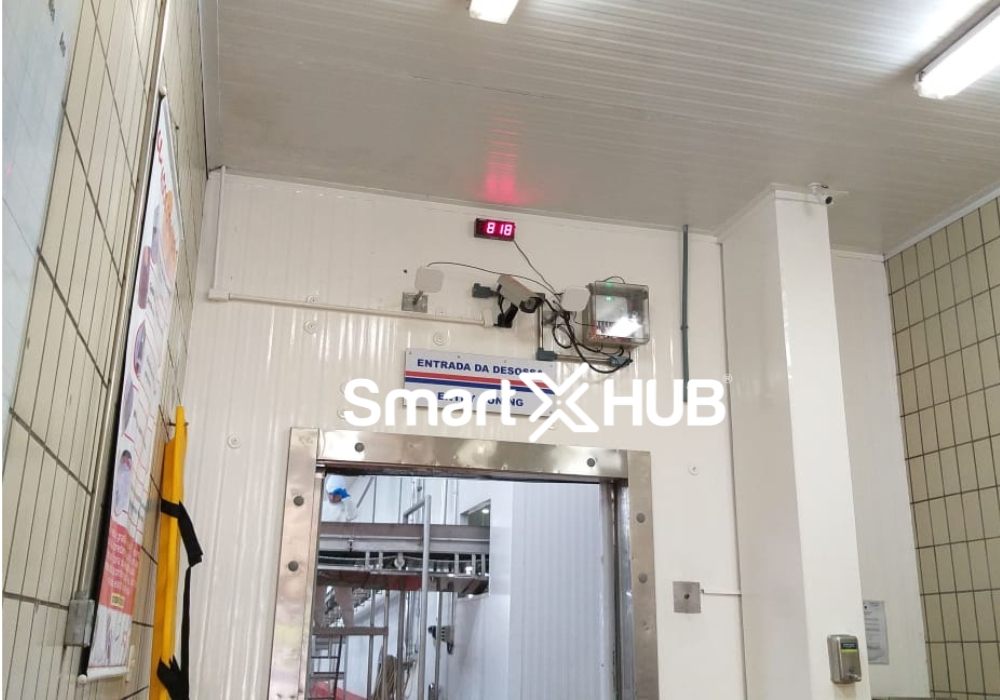
Conclusion
JBS Foods' implementation of SmartXHUB's RFID-enabled solution represents a significant advancement in workforce management and safety in the food processing industry. By ensuring compliance with NR36 regulations and integrating with HR systems, this technology enhances worker safety, productivity, and operational efficiency while mitigating legal risks. For more insights into how SmartXHUB can transform your workforce management, visit our website and explore our comprehensive solutions tailored to meet the unique challenges of the food processing industry.
For more details on this innovative project and other initiatives, visit our website and stay tuned for more updates on how our customers continues to lead in safety and operational excellence
Combining for Workplace Safety and Optimization AI and a Connected Workforce for Workplace Safety and Optimization with Smartx HUB
Designed to align with the mandates of organizations within the sector, the platform transforms smartphones and wearables into a comprehensive operational and safety tool. It empowers workers with connected insights and information, which loops back to decision-makers, creating a holistic ecosystem of data and engagement.