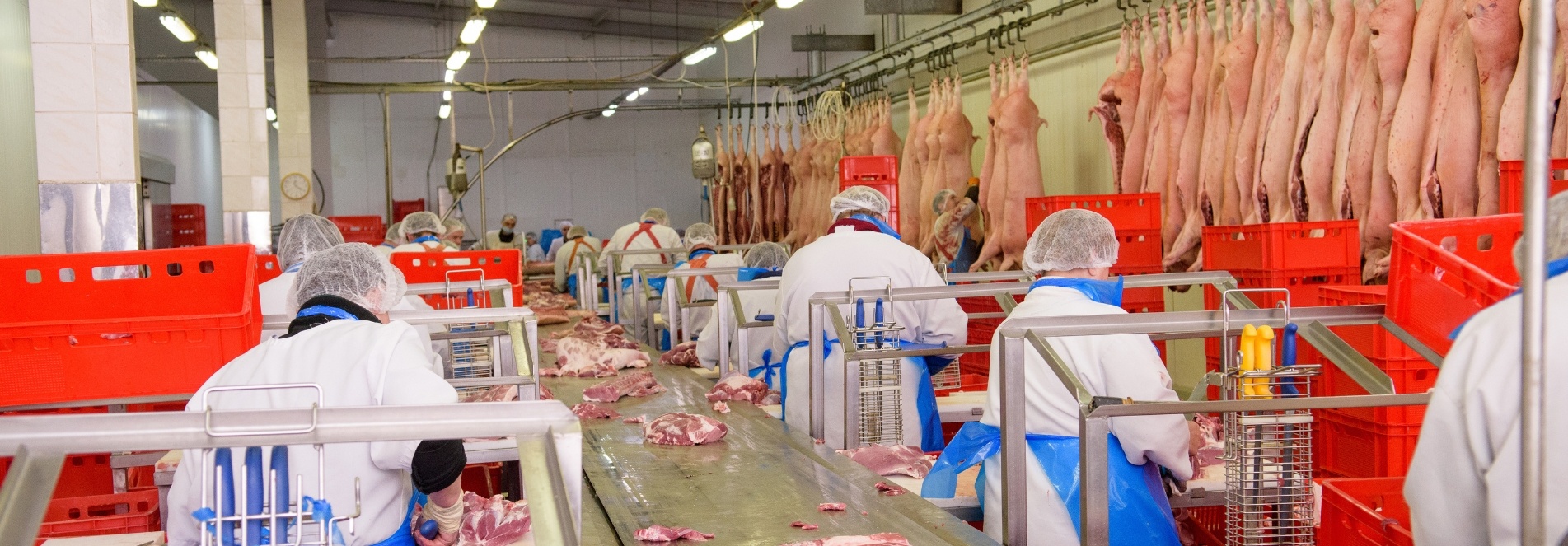
Combining AI and a Connected Workforce for Workplace Safety and Optimization
Cold Stress Safety and Manpower Capacity Monitoring with RFID Technology at Marfrig
Customer Case: Marfrig
Managing a substantial workforce in the food processing industry, particularly under the stringent NR36 regulations in Brazil, presents considerable challenges. NR36 aims to safeguard workers' health and safety in meat processing plants by enforcing strict guidelines on exposure times, rest breaks, thermal comfort, PPE, and medical monitoring. To meet these requirements, Marfrig has implemented an innovative solution using RFID technology integrated with SmartXHUB.
Marfrig Global Foods is one of the world's largest beef producers and a leading provider of lamb and poultry products. Headquartered in São Paulo, Brazil, Marfrig operates in numerous countries across the Americas, Europe, and Asia. The company employs over 32,000 people and manages more than 30 production units and distribution centers. Marfrig's extensive portfolio includes high-quality fresh and processed meat products, catering to a diverse range of customers worldwide. With annual revenues exceeding $12 billion, Marfrig is committed to sustainability, innovation, and maintaining high standards of food safety and quality throughout its operations.
The Challenge
Ensuring compliance with NR36 regulations is crucial for Marfrig, given the need to protect worker safety while managing the schedules, productivity, and wellbeing of thousands of employees across multiple shifts. Monitoring individual and collective risks, controlling entry and exit times, and guaranteeing necessary breaks are essential to maintaining a safe and productive environment. Additionally, addressing legal issues arising from occupational disease claims requires rigorous adherence to safety standards to mitigate legal and financial liabilities.
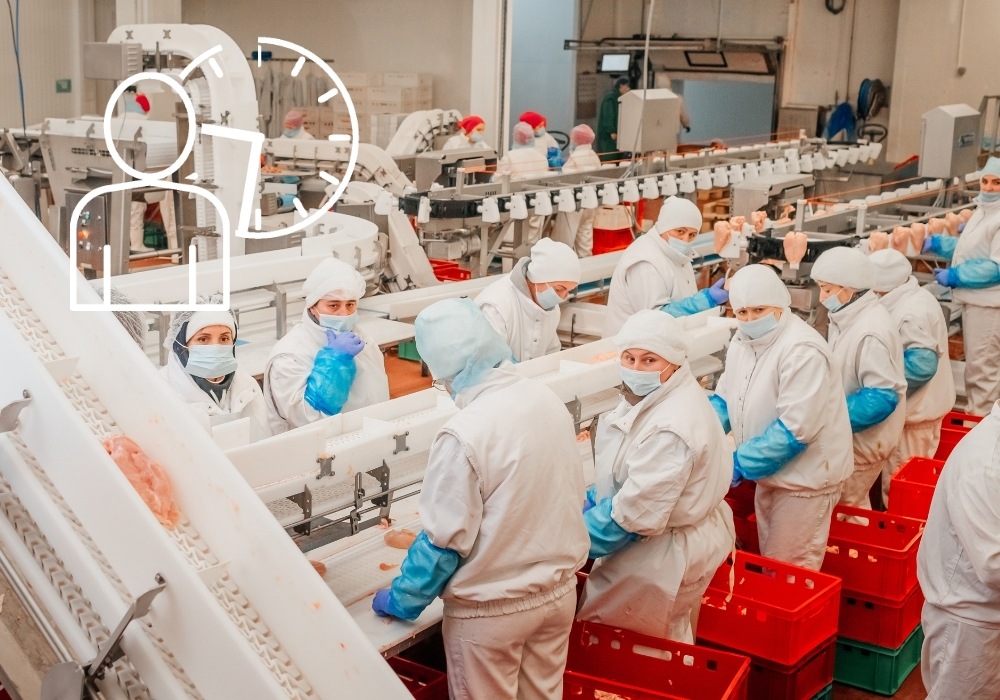
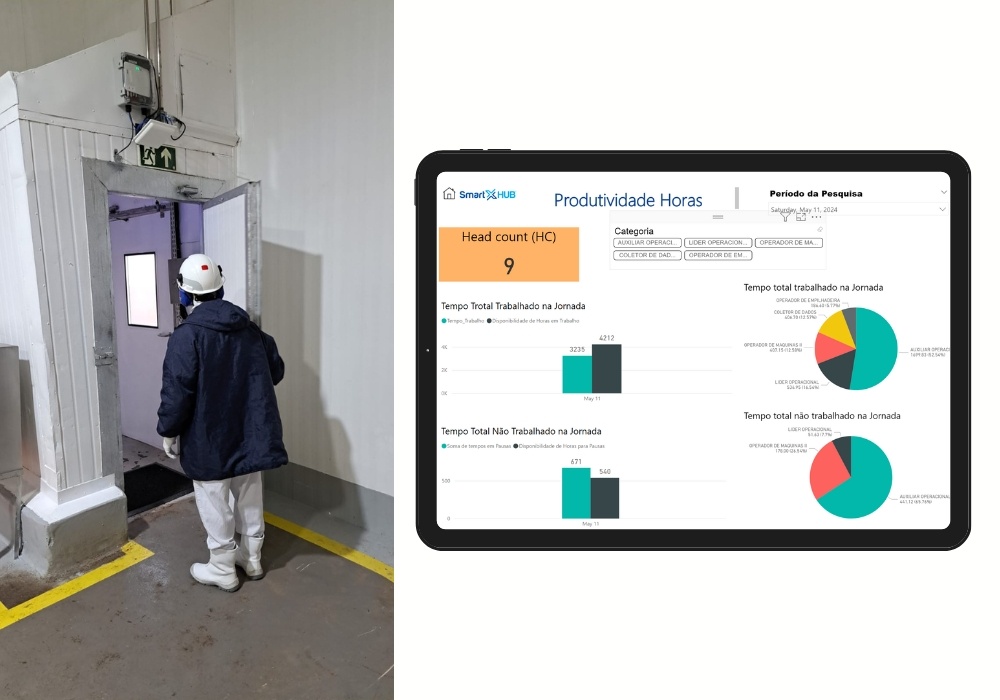
The Solution
Marfrig has adopted SmartXHUB, an advanced workforce management system that utilizes RFID technology. This system seamlessly integrates with the company’s HR solutions, offering a comprehensive approach to managing worker schedules, productivity, and safety.
Key components of the solution include:
- RFID-Enabled PPE: Workers are equipped with PPE embedded with RFID tags, allowing real-time tracking of movements and activities.
- Strategic RFID Readers: Six RFID readers are placed in key facility locations to ensure precise monitoring of entry and exit times and track worker movements within the plant.
- Integrated Management Dashboard: A centralized dashboard, accessible via a smartphone app, provides managers with real-time data on worker attendance, productivity, and compliance with safety regulations.
- PowerBI Integration: The dashboard includes integration with PowerBI, offering advanced data analytics and visualization capabilities. This allows managers to generate detailed reports, track trends, and make data-driven decisions to enhance operational efficiency and safety.
- Legal Compliance and Documentation: The system maintains detailed records of safety practices and NR36 compliance, reducing vulnerability to legal claims related to occupational diseases.
- Productivity Monitoring: The system tracks productivity metrics, enabling managers to identify inefficiencies and optimize performance.
- Paperless Time Sheet Management: Automating time sheet management eliminates over 100 pages of manual paperwork annually, streamlining administrative processes and reducing errors.
Key Benefits of SmartXHUB for Marfrig Foods
- Real-Time Monitoring and Compliance: RFID technology provides precise tracking of worker movements, ensuring compliance with NR36 regulations by monitoring exposure times, break periods, and PPE usage.
- Enhanced Safety and Risk Management: The system tracks individual and collective risks, helping prevent accidents and health issues by ensuring adherence to safety protocols and mandated breaks.
- Seamless HR Integration: SmartXHUB integrates with HR systems to manage worker schedules, certifications, and training, ensuring all personnel are qualified and compliant with safety standards.
- Operational Efficiency: Real-time data and insights allow managers to optimize workforce deployment, monitor productivity, and respond quickly to issues, enhancing overall efficiency.
- Legal Risk Mitigation: Detailed documentation and real-time compliance monitoring significantly reduce exposure to legal claims related to worker health and safety.
- Boosted Productivity: Productivity monitoring capabilities help managers identify inefficiencies and implement improvements for optimal performance.
- Paperless Operations: Automated time sheet management eliminates extensive manual paperwork, streamlining processes and reducing administrative burdens.
- Advanced Analytics with PowerBI: Integration with PowerBI provides advanced analytics and data visualization, allowing for better decision-making and strategic planning.
Implementation and Results
The implementation of SmartXHUB at Marfrig involved rigorous testing and validation to ensure the system’s reliability and effectiveness in real-world conditions. This deployment included equipping workers with RFID-enabled PPE, installing six RFID readers, and integrating the system with the existing HR platform.
The results have been impressive:
- Improved Compliance and Safety: Adherence to NR36 regulations has significantly reduced safety incidents, with all workers maintaining up-to-date certifications and training.
- Enhanced Monitoring: Real-time tracking and automated alerts provide comprehensive visibility of worker movements and safety status, enabling quick responses to potential hazards.
- Increased Operational Efficiency: The system reduces paperwork and administrative burdens, allowing staff to focus on critical tasks and improve overall productivity.
- Legal Risk Mitigation: Thorough documentation and real-time compliance monitoring significantly reduce exposure to legal claims related to worker health and safety.
- Boosted Productivity: Productivity monitoring helps managers optimize performance and address inefficiencies.
- Paperless Operations: Automated time sheet management eliminates over 100 pages of manual paperwork annually, streamlining administrative processes.
- Data-Driven Decisions: Advanced analytics and data visualization through PowerBI enable better decision-making and strategic planning.

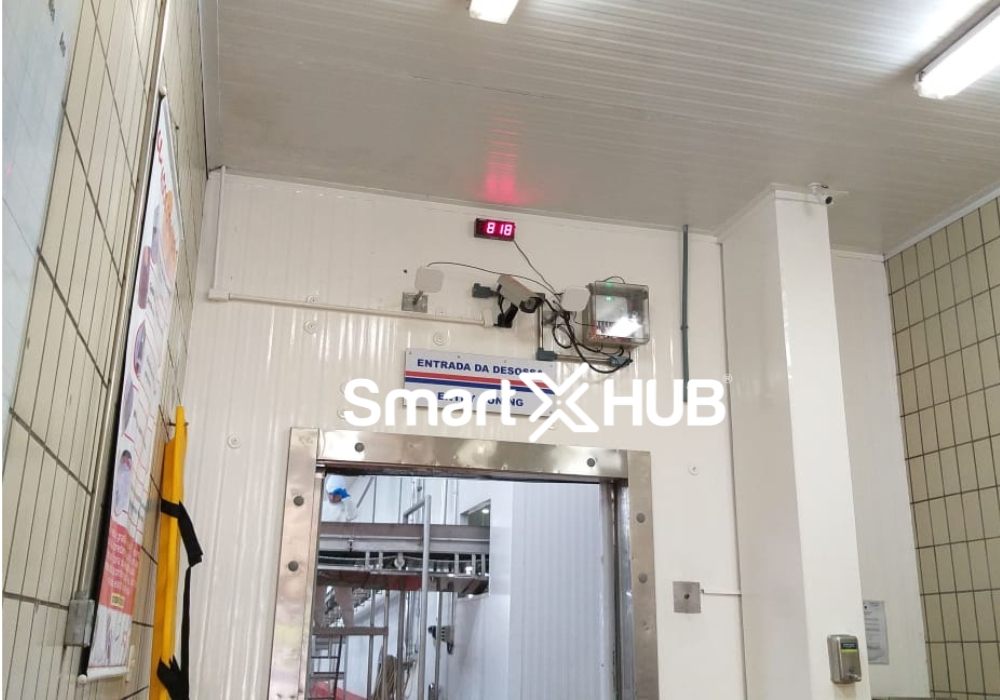
Conclusion
Marfrig’s adoption of SmartXHUB’s RFID-enabled solution marks a significant advancement in workforce management and safety in the food processing industry. By ensuring compliance with NR36 regulations and integrating with HR systems, this technology enhances worker safety, productivity, and operational efficiency while mitigating legal risks. For more insights into how SmartXHUB can transform your workforce management, visit our website and explore our comprehensive solutions tailored to the unique challenges of the food processing industry.
For more details on this innovative project and other initiatives, visit our website and stay tuned for more updates on how our customers continues to lead in safety and operational excellence
Combining for Workplace Safety and Optimization AI and a Connected Workforce for Workplace Safety and Optimization with Smartx HUB
Designed to align with the mandates of organizations within the sector, the platform transforms smartphones and wearables into a comprehensive operational and safety tool. It empowers workers with connected insights and information, which loops back to decision-makers, creating a holistic ecosystem of data and engagement.