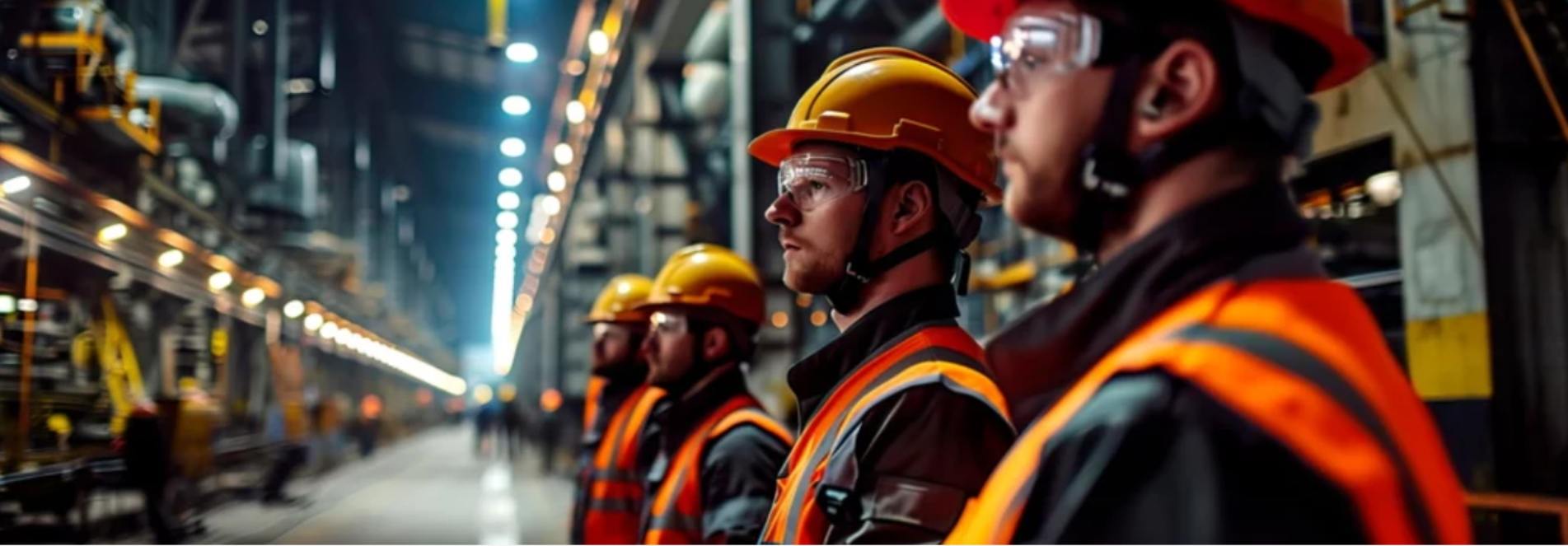
Combining AI and a Connected Workforce for Workplace Safety and Optimization
Why data and the connected worker are central to digital transformation
What is industrial digital transformation and what does it mean
Industrial digital transformation involves applying digital technologies to revolutionize traditional industrial processes and operations. This encompasses the use of technologies like the Internet of Things (IoT), artificial intelligence (AI), machine learning, and robotics to optimize manufacturing, enhance product quality, reduce costs, and boost efficiency.
However, industrial digital transformation isn't just about adopting new technologies; it requires a comprehensive approach that integrates people, processes, and technology. This includes digitizing supply chain and logistics processes, utilizing predictive maintenance to minimize downtime, and embracing new business models enabled by digital technologies.
It also involves creating a digital-first organization that empowers employees to handle more complex tasks and enables organizations across all sectors to leverage data for improving operations, competitiveness, profitability, and processes.
Moreover, industrial digital transformation presents significant opportunities for enhancing safety and reducing environmental impact. For instance, sensors and other IoT devices can monitor equipment to identify potential safety hazards before they occur, while machine learning can adapt proactively to changing conditions and processes, providing dynamic safety assessments. This helps prevent life-threatening events and production failures by implementing personalized safety routines that guide the performance of people, tasks, and assets.
How to improve chances of success
Digital transformation is not always a success story, and many companies struggle to achieve the outcomes they expect at costs they didn't predict. Here are some key considerations for companies looking to improve their chances of success:
Develop a Clear Digital Transformation Strategy: Success in digital transformation hinges on having a well-defined strategy. Identify the specific business goals you aim to achieve and create a detailed roadmap for reaching those goals. This strategy should be based on a thorough understanding of your organization’s capabilities and resources, as well as the competitive landscape and the evolving needs of your customers.
Focus on People and Culture: Digital transformation extends beyond technology; it involves people and culture as well. Foster a culture of innovation and collaboration where everyone in the organization is empowered to contribute to the transformation process. Effective change management, clear communication, and ongoing training and development are essential.
Use Data to Drive Decisions: Data is crucial for digital transformation, informing decisions at every stage. By collecting and analyzing data, you can identify opportunities for improvement, measure progress, and make informed decisions about resource allocation.
Adopt an Agile Approach: Digital transformation is an ongoing process that requires flexibility and agility. Instead of implementing a complete solution all at once, start with small, focused projects that deliver quick, tangible results. This iterative approach allows you to refine your strategy over time based on stakeholder feedback and achieved outcomes.
Collaborate with Partners and Vendors: Digital transformation often necessitates specialized expertise that may not be available in-house. Collaborate with partners and vendors who can provide the necessary skills and resources. This collaboration can accelerate your transformation efforts and yield better outcomes at a lower cost.
Empower Employees with Intelligence and Insights: A successful digital transformation involves empowering employees with the tools and insights they need to identify issues and opportunities, make informed decisions, and act quickly. Implementing connected worker solutions can enhance this empowerment, leading to more effective and responsive operations.
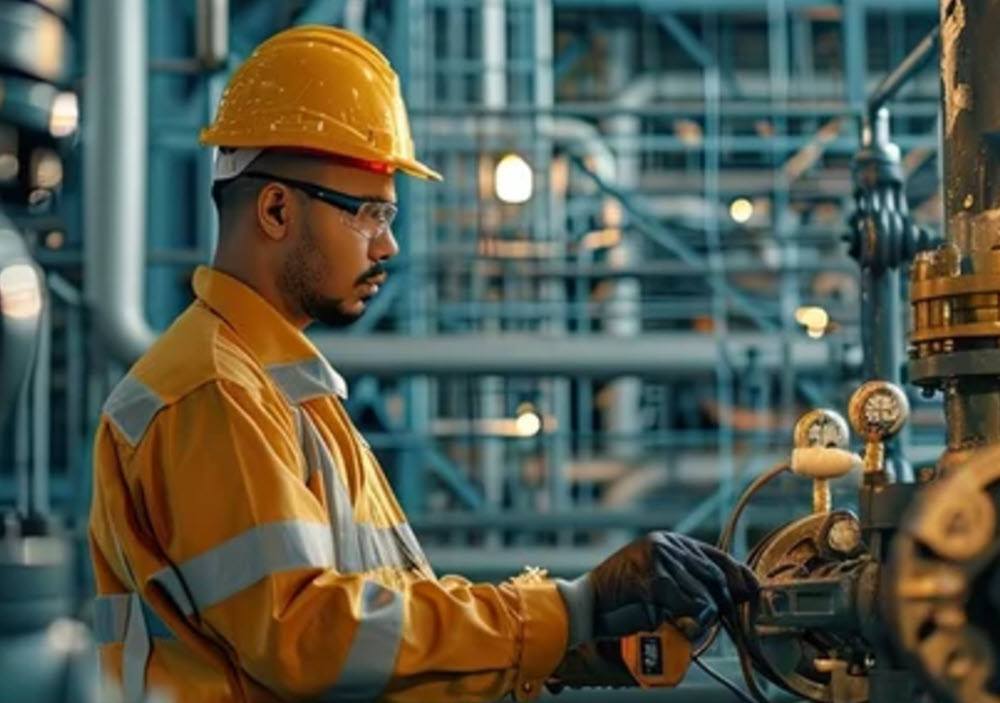
The critical importance of the Connected Worker
Empowering employees with intelligence and insights that provide transparency and visibility throughout the business is a crucial component of successful digital transformation. This is where the concept of the connected worker comes in.
The connected worker is central to the digital transformation strategy, focusing on equipping employees with the right information, tools, and technology to make better decisions and be more productive. By connecting workers to digital tools and platforms, they gain access to real-time data, analytics, and insights, enabling them to identify issues and opportunities, make informed decisions, and act quickly.
Connected workers use devices such as tablets, smartphones, wearables, and other connected devices to access critical data and communicate in real-time. This enhances efficiency, fosters effective collaboration, and keeps them informed of changing workplace conditions. Additionally, connected devices empower workers to identify potential safety hazards and take corrective action before problems arise, creating a safer and more secure work environment for both employees and the organization.
Ensuring the seamless flow of information between employees, management, and other stakeholders is essential for empowering workers to make the right decisions with the right data at the right time. By providing access to real-time data, analytics, and insights, workers can better understand the needs of the business and customers, and respond swiftly to changing conditions.
The value of data
This brings the conversation back to data, highlighting its value as a catalyst for driving the adoption and capabilities of Industry 4.0. In an industrial setting, the value of data is evident across multiple touchpoints. Data connects the digital dots, providing insights that streamline processes and improve deliverables.
It translates into real-time insights that impact decision-making, enabling immediate response times and enhancing operational performance.
Most importantly, data can be leveraged to mitigate risk and increase the value of the connected worker in an increasingly challenging environment.

Safety beyond compliance.
With Smartx HUB's connected safety solutions and data, you can review workers' risk exposure reports, analyze heat maps of hazardous incident locations, and track compliance trends over time. Unsure about the current calibration status of every critical asset in your operation? Smartx HUB provides real-time visibility into every connected device, enabling you to ensure the safety of your workers. With connected wearables that deliver data analytics for real-time compliance, you can be confident that you are not only compliant but also proactively improving the safety of your team.
Efficiently manage your workforce and trade partners using safety wearables, smart sensors, and a workforce management platform.
Combining for Workplace Safety and Optimization AI and a Connected Workforce for Workplace Safety and Optimization with Smartx HUB
Designed to align with the mandates of organizations within the sector, the platform transforms smartphones and wearables into a comprehensive operational and safety tool. It empowers workers with connected insights and information, which loops back to decision-makers, creating a holistic ecosystem of data and engagement.